It is evident that the development speed of SiC power semiconductors in recent years has almost exceeded everyone's expectations. Among them, SiC MOSFETs have attracted particular attention due to their potential to replace existing silicon super junction (SJ) transistors and IGBT technology.
Industry veterans and new players are pouring into this emerging market, doubling down on their bets.
In fact, the development history of SiC MOSFETs is quite long. John Palmour, one of the founders of Cree, the predecessor of the global SiC industry leader Wolfspeed, applied for a patent involving the creation of MOS capacitors on SiC substrates as early as 1987. This patent was later regarded as the key to the birth of SiC MOSFETs.
However, due to issues such as substrate yield and manufacturing processes, it was not until around 2010 that SiC MOSFETs officially achieved commercialization.
At that time, Cree launched the first SiC MOSFET on the market, the planar-gate structure CMF20120D (there are also claims that in 2010, Rohm was the first to launch the first planar SiC MOSFET). By 2015, Rohm was the first to achieve mass production of trench-gate structure SiC MOSFETs, which can better utilize the characteristics of SiC materials and have a more complex process.
Advertisement
After nearly 10 years of development, the trench-type SiC MOSFET is currently considered to be a more advantageous technical route and development direction on the SiC MOSFET technology path.
Planar or Trench?
In the debate over the technical route of SiC MOSFETs, there have always been two different structural types: planar gate and trench gate.
Both planar-gate and trench-gate are vertically conductive MOSFETs, with similarities in structure, where the source is on the top layer and the drain is on the bottom layer. The difference lies in the gate.
Planar-gate SiC MOSFET structure: refers to the gate electrode and the source electrode being distributed on the same horizontal plane as a "planar" layout, with the channel parallel to the substrate. The characteristic of the planar-gate structure is that the process is simple, the consistency of the unit is good, and the avalanche energy is relatively high. However, due to the presence of the JFET region, the input capacitance of the planar-gate SiC MOSFET device is larger, which increases the on-state resistance and reduces the current capability of the device.Trench-type SiC MOSFET Structure: This refers to a structure where the gate is located below the source, forming a "trench" in the semiconductor material. In the trench gate structure, the channel and the gate are perpendicular to the substrate, which is a significant difference from the planar gate structure. Although its process is more complex and the unit consistency is worse than the planar structure, the trench structure does not have the JFET effect, has a higher channel density, and the SiC crystal plane where the channel is located has a higher channel mobility. Therefore, it can achieve a lower specific on-resistance, enabling larger current conduction and a wider switching speed.
As a result, the new generation of SiC MOSFETs mainly researches and adopts this structure.
In comparison, the planar gate SiC MOSFET process is less complex, and its development history is longer. Domestic and foreign related products have been mass-produced earlier, and driven by many car companies such as Tesla and BYD, the planar gate SiC MOSFET power module has been used in the main drive inverter since 2018.
However, in the process of reducing the chip size to improve the yield, the lateral topology of the planar gate SiC MOSFET limits the extent to which it can be reduced.
In contrast, the trench-type SiC MOSFET devices, due to the adoption of the trench gate structure, have the following prominent advantages:
The conductive channel changes from horizontal to vertical, effectively saving the device area and greatly improving the power density;
The trench structure almost eliminates the JFET region, which greatly reduces the input capacitance of the device, improves the switching speed, and reduces the switching loss;
The JFET region resistance is also eliminated, and the device Rdson can be further improved with lower current capability.
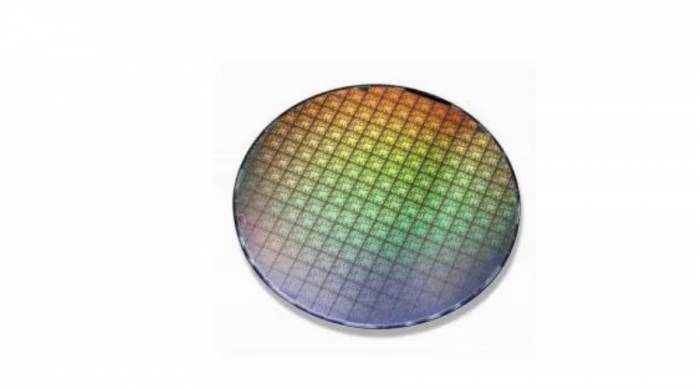
Compared with the planar gate SiC MOSFET devices, the trench-type SiC MOSFET has a larger power density, faster switching speed, lower on-resistance, and lower loss, thus attracting high attention from the industry.In layman's terms, a trench-gate SiC MOSFET can be understood as "digging holes" on the basis of a planar structure. International SiC manufacturers are leveraging the potential of SiC more effectively through trench-gate technology. Although everyone is "digging holes," the methods vary slightly. Looking around, some manufacturers dig one hole, some dig two, and others dig at an angle. Various technical structures emerge endlessly, presenting a hundred flowers blooming together.
For this reason, SiC chip suppliers, especially international giants, are leveraging their respective strengths and have started exploring trench-type SiC MOSFETs.
Trench-type SiC MOSFETs, multi-faceted initiatives
Among the leading SiC device suppliers, almost all have begun to deploy trench-gate MOSFETs.
ROHM and Infineon were the first companies to turn to trench SiC MOSFETs. According to Yole's report, the trench SiC MOSFET camp has expanded from the original ROHM and Infineon to several leading giants, such as Sumitomo Electric, Mitsubishi Electric, Denso, Qorvo (UnitedSiC), ST, Wolfspeed, ON Semiconductor, and so on, all transitioning from planar structure MOSFETs to trench structures.
ROHM: Dual trench structure
In 2015, ROHM developed and mass-produced the world's first trench-structured SiC MOSFET, which is a dual trench structure. To date, ROHM's trench-type SiC MOSFET has evolved to the fourth generation, with both source and gate trenches.
In a typical single trench structure, the electric field is concentrated at the bottom of the gate trench, which has always been a concern for long-term reliability. The dual trench structure developed by ROHM also has a trench structure in the source area, which alleviates the concentration of the electric field at the bottom of the gate trench. This structure has successfully reduced the electric field, preventing damage to the oxide layer at the gate trench, ensuring long-term reliability, and improving device performance.
It is understood that in the fourth-generation SiC MOSFET, ROHM has further improved the dual trench structure. It has successfully reduced the on-resistance by about 40% compared to the third-generation product while improving the short-circuit withstand time; at the same time, by significantly reducing the gate leakage capacitance, it has successfully reduced the switching loss by about 50% compared to the third-generation product.Rohm predicts that from 2023 onwards, the proportion of the 4th generation SiC MOSFET in its sales composition will gradually increase, and it will become the mainstay of sales in 2024-2025.
Compared with competitors who are still challenging the first mass-produced trench gate products, Rohm has taken the lead by several steps. According to its product roadmap, it is expected that the 5th and 6th generation products to be launched in 2025 and 2028 will respectively reduce the on-resistance by another 30%.
Infineon: Semi-encapsulated trench structure
As we all know, "digging a pit" is Infineon's traditional craft.
In the era of silicon-based products, Infineon's trench-type IGBT and trench-type MOSFET were unparalleled. With the advent of the SiC era, most SiC MOSFETs on the market are planar cell types, while Infineon still continues the route of trench structure.
In 2017, Infineon reported a trench-type SiC MOSFET device with a semi-conducting structure, forming a conductive trench channel on one side of the gate trench. From the above figure, it can be seen that the doped area adjacent to the trench is asymmetrical, and the left wall of the trench contains the MOS channel, which is aligned to the a-plane to achieve the best channel mobility. Most of the bottom of the trench is embedded in the p-type region below the bottom of the trench.
This structure can protect the trench corners from the impact of the peak electric field, improve the reliability of the device, and further enhance the voltage withstand capability of the device, making the switching control good and the dynamic loss very low. In particular, this characteristic is crucial for suppressing the additional loss caused by parasitic conduction in the topology using a half-bridge.
Infineon's CoolSiC MOSFET trench discrete device series, using Infineon's unique trench method, brings many benefits to its system design, including high reliability, efficiency improvement, achieving high switching frequency and high power density, reducing system complexity and total system cost.Infineon introduced its first generation of CoolSiC series SiC MOSFETs in 2016 and updated the second generation of products in 2022, which enhanced the carrying current capacity by 25%-30% compared to the first generation.
In terms of production capacity, Infineon currently mainly uses its unique "cold cutting" technology to reduce material waste during the crystal ingot cutting process, which can double the production capacity by obtaining twice as many silicon carbide substrates from the same crystal ingot in the future. On the other hand, Infineon announced an investment of over 2 billion euros last year to expand its wafer factory in Malaysia, specifically targeting the expansion of silicon carbide wafers.
STMicroelectronics: Deeply exploring the potential of planar technology and laying out trenches
According to Yole data statistics, the company with the highest market share of global silicon carbide power devices is STMicroelectronics (ST). At the same time, with the cooperation with Tesla, ST's SiC MOSFET products were also the earliest to be applied on a large scale in electric vehicles. Since the Model 3 model, Tesla has been using ST-supplied silicon carbide modules on a large scale.
In terms of chip design, STMicroelectronics continues to deeply explore the technical potential of planar silicon carbide MOSFETs, and launched the 4th generation planar gate SiC MOSFET in 2022. Compared with the previous generation of products, the performance of the 4th generation planar gate silicon carbide has improved, including a 15% reduction in on-resistance and a doubling of the operating frequency to 1MHz.
The previously planned trench gate products have been postponed to become the 5th generation SiC MOSFET of STMicroelectronics, which is currently in the research and development stage and is expected to be mass-produced in 2025.
Compared with planar SiC MOSFETs, trench-type SiC MOSFETs can have smaller on-resistance, smaller parasitic capacitance, and stronger switching performance.
In terms of production capacity, ST previously planned to invest $2.1 billion in the 2022 fiscal year to expand production capacity, including expanding the original 6-inch silicon carbide wafer factory and the 6-inch silicon carbide wafer factory in Singapore that started operation in 2022. At the same time, Norstel, a Swedish silicon carbide substrate manufacturer acquired by ST in 2019, has also started testing 8-inch silicon carbide materials, and it is expected to be applied in the 8-inch production line in Singapore around 2025.
ON Semiconductor: Trench-type products are imminentIn the third quarter of 2021, with the acquisition of substrate supplier GTAT, ON Semiconductor established a vertically integrated model from silicon carbide ingots, substrates, device production to module packaging.
Although some of the technical strengths of the projects are still lagging behind leading enterprises in various fields, their overall strength is more balanced: compared with the substrate leader Wolfspeed, ON Semiconductor's module packaging and mass production experience is slightly better; compared with Infineon, which has outstanding device design strength, ON Semiconductor has the advantage of GTAT's silicon carbide materials.
From the perspective of product structure, ON Semiconductor's first-generation silicon carbide MOSFET technology (M1) adopts a planar design with a voltage rating of 1200V. Subsequently, specifications with voltage ratings of 900V and 750V were derived, and the microstructure was changed to Hex Cell design. The combination of these two changes reduced the on-resistance of the silicon carbide MOSFET by about 35%. At present, most of the silicon carbide products launched by ON Semiconductor are based on the M1 platform and its derived M2 platform.
The latest generation of silicon carbide technology (M3) still adopts planar technology, but has changed to the patent-protected Strip Cell design, and the on-conductivity has been improved by 16% compared to the previous generation of derivatives. This generation of products will gradually become the company's main automotive-grade silicon carbide platform, covering the mainstream 400V and 800V platforms of electric vehicles in terms of voltage specifications.
It is understood that ON Semiconductor's next-generation technology platform M4 will upgrade from planar structure to trench structure. Compared with the first-generation silicon carbide technology, the trench-structured SiC MOSFET can reduce the chip area by a considerable amount under the same current requirements. If the M4 platform is also expected to use 8-inch wafer production, the cost of M4 is expected to be significantly reduced compared to the previous one.
In fact, ON Semiconductor has been researching trench gates for many years, and many samples are undergoing internal testing. The only problem they believe is that the premature launch of trench gate products still carries certain risks in terms of reliability. Therefore, ON Semiconductor is optimizing reliability and improving the utilization rate of trench gates.
At the same time, in terms of improving reliability, ON Semiconductor is also exploring the bottom line of trench gates, adding some test points that are considered risky on the basis of standard testing, in an effort to clarify the risks.
In addition, from the packaging perspective, ON Semiconductor provides various packaging options and will also launch the next generation of packaging with strong design, adapting to different needs through continuous iteration of packaging.
Mitsubishi Electric: Unique Electric Field Restriction StructureIn 2019, Mitsubishi Electric also developed a trench SiC MOSFET. To address the issue of gate insulating film fracture in trench-type structures under high voltage, Mitsubishi Electric developed a unique electric field limiting structure based on advanced simulations conducted during the structural design phase. This structure reduces the electric field applied to the gate insulating film to the level of conventional planar types, thereby enhancing the reliability of the gate insulating film under high voltage.
Mitsubishi Electric ensures device reliability with its unique electric field limiting structure. By injecting aluminum and nitrogen, the electrical properties of the semiconductor layer are altered to protect the gate insulating film.
Specifically, aluminum is injected in the vertical direction of the trench, forming an electric field limiting layer at the bottom of the trench. Then, using its new oblique injection technology of aluminum, a side ground connection is formed between the electric field limiting layer and the source, and nitrogen is obliquely injected to form a high-concentration doped layer that is easier to conduct electricity locally. The electric field limiting layer reduces the electric field applied to the gate insulating film to the level of traditional planar structures, ensuring voltage resistance while improving device reliability. The side ground connection between the electric field limiting layer and the source enables high-speed switching actions, reducing switching losses.
Compared to planar structures, trench-type devices have a smaller cell pitch, allowing power devices to arrange more cells. The high-density arrangement of cells increases the flow of current, but the narrow spacing between each gate can lead to a narrower path and difficulty in current flow. Oblique injection of nitrogen forms a high-concentration doped layer that is easier to conduct electricity locally, making the current on the current path easier to transmit, thereby reducing the resistance of the electrical path. Compared with no high-concentration layer, the resistivity is reduced by about 25%.
Wolfspeed: The advantages of planar gate SiC MOSFETs are not exhausted.
As a company that has been in the SiC industry for over 30 years, Wolfspeed and its predecessor Cree launched the first mass-produced silicon carbide substrate in 1991. The profound experience and historical accumulation have made Wolfspeed's silicon carbide substrate performance and quality unparalleled, even competitors such as STMicroelectronics, Infineon, and ON Semiconductor have to spend hundreds of millions of dollars to purchase from it. Therefore, Wolfspeed's silicon carbide products have gained a crucial first-mover advantage and have become a benchmark for the entire silicon carbide industry.
In terms of design, Wolfspeed's silicon carbide MOSFETs adopt planar design, currently in the 3rd generation, covering multiple voltage specifications between 650V and 1200V. Compared with the previous two generations, the Gen3 planar MOSFET adopts a hexagonal cell microstructure, and the on-resistance is reduced by 16% compared to the previous generation Strip Cell.
It is understood that Wolfspeed's next-generation product will be a trench gate design. Currently, the Gen4 trench gate MOSFET is still under development, and the specific mass production time has not been disclosed.Despite also laying out trench structures, Wolfspeed, which has been committed to the development of silicon carbide diodes and MOSFETs from the beginning, believes that the technical advantages of planar-gate SiC MOSFETs are far from exhausted.
Wolfspeed co-founder John Palmour once said: "Because trench MOSFETs have better on-resistance, which is a key performance indicator. As long as we are far ahead in on-resistance compared to trench SiC MOSFETs, I don't think there is any reason to change this, let alone we will continue to improve the planar SiC MOSFET. Customers should not care whether it is a planar MOSFET or a trench MOSFET, what matters is the specific on-resistance. In fact, we also don't care which technical route, we only focus on which design can bring the greatest benefits to customers."
In short, there is still room for deep exploration of the planar structure, and doing a good job in reliability also has a market.
Fuji Electric: Full SiC Trench MOSFET
As early as 2016, Fuji Electric developed a 1200V SiC trench MOSFET for full SiC modules, achieving a low specific resistance of 3.5mΩcm², a threshold voltage of 5V, while maintaining the high reliability of the "channel" used to turn on and off the current.
As a result, compared with the previous planar structure, the resistivity was successfully reduced by more than 50%. In addition, Fuji Electric has also developed a high current density dedicated SiC module with a unique pin connection structure, fully utilizing the advantages of SiC devices. Fuji Electric has used this device to achieve an All-SiC module.
Sumitomo Electric: V-shaped Trench
In 2016, Sumitomo Electric developed a V-shaped trench SiC MOSFET device sample with a thick bottom oxide layer, further improving the gate oxide reliability and threshold stability of the device.
Sumitomo Electric has newly developed a V-shaped trench MOSFET using a unique crystal plane. The V-MOSFET has superior characteristics such as high efficiency, high blocking voltage, and high stability under harsh conditions, achieving a large current (single chip 200A), suitable for EV and HEV. In addition, Sumitomo Electric is collaborating with the National Institute of Advanced Industrial Science and Technology to develop the next generation of V-MOSFETs with the world's lowest on-resistance.Denso of Japan: U-shaped Trench
In March 2023, Denso (DENSO) announced the development of its first inverter using SiC semiconductors.
The unique trench-type MOS structure of Denso, which employs its patented electric field mitigation technology in trench gate semiconductor devices, has increased the output per chip. This is because they reduce power loss caused by heat generation, and the unique structure achieves high voltage and low on-resistance operation.
Some information shows that Denso's trench structure is similar to that of Sumitomo, but it has been changed to a U-shaped trench.
Qorvo: High-density Trench SiC JFET Structure
Qorvo's SiC technology mainly comes from the acquisition of UnitedSiC in 2021, and SiC is also a top priority for Qorvo's future development.
It is understood that different from the traditional SiC MOSFET design, Qorvo has taken a new path. Its SiC MOSFET uses a high-density trench SiC JFET structure, where the channel resistance Rchannel in the SiC MOSFET is replaced by the resistance of the low-voltage silicon MOSFET in the SiC FET. The latter has a much better inversion layer electron mobility, achieving an ultra-low specific area on-resistance, and therefore the loss is also lower. This structure is packaged together with the low-voltage Si MOSFET, and the chip area of the SiC FET is also relatively small.Qorvo has expanded its 1200V product series by extending its breakthrough fourth-generation SiC FET technology to higher voltage applications, with product specifications ranging from 23mΩ to 70mΩ, targeting the 800V electric vehicle onboard charger (OBC) and DC converter markets.
Renesas Electronics: Periodic Connection, Variant Dual-Grade Trench MOSFET
It is understood that Renesas Electronics has just applied for a patent in 2023 to research silicon carbide trench structures, referred to as "Periodic Connection, Variant Dual-Grade Trench MOSFET."
In conclusion, several key indicators for improving the performance of SiC MOSFETs, including smaller cell spacing, lower specific on-resistance, lower switching losses, and better gate oxide protection, all point towards the trench gate structure.
From an industry perspective, the main manufacturers of mass-produced trench-type SiC MOSFETs are international SiC manufacturers from Europe, the United States, and Japan. Looking at the layout of international manufacturers, trench gate SiC MOSFETs will be a more competitive solution in the future.
Since the launch of the first mass-produced trench gate SiC MOSFET product in 2015, nearly nine years have passed, and many companies are developing trench gate products, but there are not many manufacturers that can currently launch mass-produced products.
Of course, designing and manufacturing high-performance trench gate SiC MOSFETs is also an urgent task for the development of domestic SiC power devices, and some companies have shifted their research focus to trench gate SiC MOSFETs. However, it should be noted that international SiC giants have been laying out in the field of SiC MOSFETs for many years and have accumulated a large number of patents. The high patent barriers of trench structures are also a hurdle that domestic manufacturers need to overcome.
According to the author of "Silicon Carbide Chip Learning Notes": "The complete process and structural IP of trench SiC MOSFETs are the entry tickets for silicon carbide competition in the next ten years!" In the current period of continued high-speed growth in the overall SiC market, laying out the right technical route in advance is the only way to seize the opportunity in future new application markets.
Post a comment