In the year that has just passed, we have all witnessed the rise of advanced packaging.
As Moore's Law gradually becomes less effective and the progress of advanced process technology slows down, advanced packaging has emerged as a dark horse, becoming the focus of the semiconductor industry. Under the huge demand in fields such as AI, cloud computing, and new energy, it has driven the rapid development of the entire semiconductor packaging industry.
Not only traditional packaging companies, but many companies that were originally focused on foundry also began to enter this market. From TSMC's CoWoS, to Intel's EMIB, to Samsung's X-Cube, various 2.5D and 3D packaging have emerged one after another and are becoming mature. In this blue ocean of packaging, a heat like a thousand sails competing has been ignited.
What is more worth paying attention to is that in order to develop the market and meet the needs of different customers, the giants are not stingy in spending billions or even tens of billions to expand and build new packaging plants. A packaging plant competition has already begun.
TSMC
TSMC settled two packaging plants in 2023, one in Zhunan and one in Zhuke.
The first is the advanced packaging and testing plant that has been put into operation in Zhunan. On June 8, 2023, TSMC's advanced packaging and testing plant in Zhunan was officially put into operation. The plant is located in the Zhunan Science Park, covering an area of 14.3 hectares. Its main focus is on next-generation high-performance computing, artificial intelligence, and mobile devices, etc., and started construction in 2020, which is currently the largest packaging and testing plant of TSMC.
Advertisement
This is TSMC's first all-in-one automated advanced packaging and testing plant that integrates front and back-end processes and testing. TSMC said that this will lay the foundation for the mass production of TSMC-SoIC process.
TSMC said in a statement that the advanced packaging and testing plant will enable the company to have more complete and flexible SoIC, InFO, CoWoS and other 3D Fabric advanced packaging and silicon stacking technology capacity, and bring higher comprehensive benefits to production yield and product performance.TSMC points out that the cleanroom area of this factory is larger than the sum of the cleanroom areas of all other TSMC packaging plants, and it is expected to process more than one million 300mm wafers annually, with annual testing service time exceeding 10 million hours. Previously, due to a severe shortage of advanced packaging capacity, TSMC squeezed a large number of orders from GPU suppliers such as Nvidia.
Then there is Hsinchu Science Park, where TSMC officially confirmed on July 25, 2023, that in response to the demand for advanced packaging such as CoWoS for AI chips from manufacturers such as Nvidia and AMD, it will invest 90 billion New Taiwan dollars to build an advanced packaging plant in Tongluo Township, Miaoli County.
It is revealed that the Hsinchu Science Park Administration has agreed to allocate 7 hectares of land, with the plant scheduled to be completed by the end of 2026, and mass production will start in the third quarter of 2027. This packaging plant has a monthly capacity of 110,000 12-inch wafers for 3D Fabric process technology, mainly providing "Chip on Wafer on Substrate" (CoWoS) packaging. After completion, it can create 1,500 job opportunities.
It is worth mentioning that there was also news that TSMC is planning to build the 7th advanced packaging and testing factory in the Taichung area, and is currently evaluating the Chiayi Science Park and Yunlin. Although it has not been officially confirmed, it also reflects the tight capacity of TSMC's advanced packaging from another perspective.
Intel
Although Intel does not have a large number of packaging orders from foundry customers like TSMC, its demand for packaging is not less at all.
On May 3, 2021, Intel announced an investment of $3.5 billion to expand the Rio Rancho factory in New Mexico, mainly to upgrade the factory's EMIB and Foveros 3D packaging technology. On January 24 this year, Intel's Rio Rancho factory Fab 9 was officially expanded.
Intel said that the factory includes Intel's breakthrough 3D packaging technology Foveros, which provides flexible options and costs for combining multiple chips optimized for power consumption and performance. The Fab 9 and Fab 11x factories in Rio Rancho are the first operational bases for large-scale production of Intel's 3D advanced packaging technology. This is also the first large-scale advanced packaging factory in the same location for Intel, marking the end-to-end manufacturing process that creates a more efficient supply chain from demand to the final product.
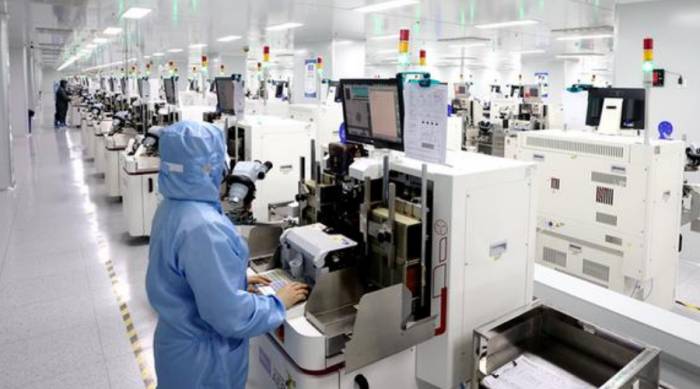
Fab 9 will help promote the next era of Intel's advanced packaging technology innovation. As the semiconductor industry enters the heterogeneous era of using multiple "chiplets" in packaging, advanced packaging technologies such as Foveros and EMIB (Embedded Multi-die Interconnect Bridge) provide a faster and more cost-effective way to achieve the 1 trillion dollar goal, extend the transistors on the chip, and extend Moore's Law beyond 2030.
In addition to New Mexico, Intel also has a layout in Malaysia. Currently, Intel has four factories in Malaysia, including two packaging and testing factories in Penang and Kulim, as well as the System Integration and Manufacturing Services (SIMS) and the in-house equipment factory (KMDSDP) in Kulim, which are responsible for the production and testing equipment.Intel announced in 2021 a $20 billion investment in the IDM 2.0 plan, of which $7 billion will be used in Malaysia. They are currently building two packaging and testing plants in Penang and Kulim, Malaysia. The packaging and testing plant in Penang will produce the most advanced 3D IC packaging Foveros in the future, which is expected to be put into use in 2024 or 2025. This will be Intel's first overseas advanced 3D packaging plant with Foveros technology after the plants in Oregon and New Mexico in the United States. It is worth mentioning that Intel also has a research and development center in Penang. In other words, the facilities that Intel has invested in Malaysia are almost a "mini Intel," except that there is no wafer foundry, highlighting the extremely important position of Malaysia to Intel.
In addition, on June 16, 2023, Intel also announced that it will invest $4.6 billion in Wroclaw, Poland, to build a new advanced packaging and testing plant, which will help meet Intel's critical demand for packaging and testing capabilities by 2027. The design and planning of the plant will start immediately, and construction will start after approval by the European Commission. It is expected to create about 2,000 jobs after completion.
After Intel expanded its foundry scope and allowed customers to purchase advanced packaging separately, it is believed that it can make better use of the production capacity of the newly built packaging and testing plants.
Samsung
Due to the popularity of HBM, Samsung is also expanding its packaging capacity in all directions.
Domestically in South Korea, Samsung Electronics invested 10.5 billion won to acquire the factory and equipment of Samsung Display in Cheongju, South Korea, to expand the production capacity of HBM. At the same time, it also plans to invest between 70 billion and 100 billion won to build a new packaging line.
Abroad, according to Japanese media citing five sources, Samsung is considering establishing a chip packaging and testing production line in Japan to strengthen its advanced packaging business and establish closer ties with Japanese semiconductor material and equipment suppliers.
Sources pointed out that the location of Samsung's new packaging and testing plant may be in Kanagawa Prefecture, Japan, because Samsung already has a research and development center there. Although the timing and other details have not been determined, the investment is likely to be tens of billions of yen (about 75 million US dollars).
Samsung is still focusing on HBM as a whole. The trend of artificial intelligence has not gone far, and the expansion and construction of new production lines and factories can better meet customer needs.Hynix
Similar to Samsung, Hynix is focusing its attention on High Bandwidth Memory (HBM). In June 2023, according to South Korean media reports, due to the increased demand for AI semiconductors, one of the leading memory companies, Hynix, is expanding its HBM production line, with plans to double its HBM production capacity. The focus of the expansion is on HBM3, and Hynix is preparing to invest in back-end process equipment to expand the packaging of HBM3 at the Icheon factory. It is expected that by the end of this year, the scale of the back-end process equipment will increase by nearly half.
Abroad, Hynix previously stated that it would invest $15 billion in the United States to establish an advanced packaging facility. According to sources, the factory is expected to achieve mass production in 2025-2026 and plans to recruit 1,000 workers. In addition, the factory will be used to package Hynix's own memory chips and logic chips designed by other American companies for machine learning and artificial intelligence applications.
Micron
Compared with Hynix and Samsung, Micron, located in the United States, is a bit more aggressive. Last year alone, Micron had four packaging plants that were expanded and newly built.
On June 16, 2023, Micron announced plans to invest more than 4.3 billion yuan in its packaging and testing factory in Xi'an, China, over the next few years. The announcement stated that Micron has decided to acquire packaging equipment from Powertech Semiconductor (Xi'an) Co., Ltd. (Powertech Xi'an) and plans to expand the new plant at the Micron Xi'an factory, introducing new and high-performance packaging and testing equipment to better meet the needs of Chinese customers.
The newly announced expansion of the new plant will introduce a new production line for manufacturing mobile DRAM, NAND, and SSD products, to enhance the existing packaging and testing capabilities of the Xi'an factory. It is reported that Micron has been preparing for this project for some time and has started the qualification certification work for the production of mobile DRAM in Xi'an.
On June 22, 2023, Micron invested $825 million in the construction of a new chip packaging and testing factory in Gujarat, India. The factory will achieve assembly and testing manufacturing of DRAM and NAND products, focusing on converting storage wafers into Ball Grid Array (BGA) integrated circuit packaging, storage modules, and solid-state drives, and meeting the needs of both domestic and foreign markets.
It is reported that the new packaging and testing facility of Micron in Gujarat is expected to start phased construction in 2023. The first phase will include a packaging and testing plant with 500,000 square feet of cleanroom space, which will start operation at the end of 2024. Micron will gradually increase production capacity over time according to global demand trends. Micron estimates that the second phase of the project will start in the second half of 2020-2030, which includes the construction of a facility similar in scale to the first phase.In October 2023, Micron Technology announced the completion of its new packaging and testing plant in Batu Kawan, Penang, Malaysia. This is the company's second packaging and testing factory in Malaysia, with an investment of $1 billion. Micron stated that it will continue to increase its investment by another $1 billion in the next few years, expanding the factory area to 1.5 million square feet. After the expansion, Micron will be able to increase production capacity and further strengthen its assembly and testing capabilities, enabling it to provide leading NAND, PCDRAM, and SSD modules to meet the growing demand for transformative technologies such as artificial intelligence, autonomous driving, or electric vehicles.
In November 2023, Micron's advanced packaging and testing plant in Taichung (Taichung Plant 4) was officially completed and opened. The factory mainly focuses on memory advanced packaging and will be an important base for the development of Micron's 1-gamma advanced process and HBM3E high-bandwidth memory advanced packaging.
ASE Technology
ASE Technology, the world's largest packaging and testing company, has set its sights on Southeast Asia and is actively expanding the production capacity of its Malaysian packaging and testing plant.
In November 2022, ASE Technology started construction of the new Plant 4 and Plant 5 in Penang, Malaysia, which is expected to be completed in 2025. After the completion of the two plants, the total construction area will reach 2 million square feet, double the existing plant area. ASE Technology pointed out at the time that it would invest $300 million within 5 years to expand the Malaysian production plant, purchase advanced equipment, and train more engineering talents.
In January of this year, ASE Technology announced that the Plant 4 and the new visitor center in Penang, Malaysia, held a grand opening ceremony. Plant 4 in Penang mainly focuses on copper clip and image sensor packaging production lines and will also layout advanced packaging products. Currently, ASE Technology's packaging and testing plant in Penang, Malaysia, includes lead frame packaging, wire bonding BGA packaging, flip chip packaging, memory packaging, and wafer-level chip-scale packaging (WLCSP), etc.
It is worth mentioning that on January 19, ASE Technology announced that its Malaysian subsidiary invested 69.696 million Malaysian ringgit (about 464 million New Taiwan dollars) to obtain the land use right of the Guihua City Science and Technology Park in Penang, Malaysia, to meet the operational needs. Industry insiders analyzed that ASE Technology's investment project also laid out advanced packaging.
Amkor Technology
Amkor Technology, the world's second-largest packaging and testing manufacturer, is expanding in all directions, establishing new plants in Vietnam, the United States, and Europe.
In October 2023, Amkor Technology's advanced packaging and testing plant in Bac Ninh Province, Vietnam, was completed and put into operation. According to Amkor Technology, its Vietnamese park is located in the An Phong II-C Industrial Park, covering an area of 57 acres, and will become the largest factory of Amkor Technology.Previously, Amkor Technology indicated that the first phase of the new factory will focus on providing advanced system-in-package (SiP) packaging and testing solutions for the world's leading semiconductor and electronics manufacturing companies. The estimated investment for the first phase is about 250 million US dollars, with a cleanroom area of approximately 20,000 square meters.
In December 2023, Amkor announced that it would invest 2 billion US dollars to build a new advanced semiconductor packaging and testing facility in Peoria, Arizona, USA, which can create up to 2,000 jobs. Production is expected to start in the next two to three years, and the facility will package and test chips produced by the nearby TSMC factory.
Amkor stated that after the new factory opens, Apple will become the first and largest customer. The factory will also provide services to other companies and will use the facility to package other chips. The first phase of the new factory is expected to start production in the next two to three years, and it has applied for subsidy funds from the "Chips Act." At least 25 billion US dollars of the 52 billion US dollars in subsidies from the "Chips Act" has been designated for the "National Advanced Packaging Manufacturing Program," and the new factory is expected to receive subsidies.
On January 16th of this year, Amkor and GlobalFoundries held a ribbon-cutting ceremony for the Porto factory in Portugal. The ceremony marked the official launch of the cooperation between the two companies, which was previously announced, and emphasized the collaboration to create a complete European supply chain for semiconductor wafer production.
GlobalFoundries stated that last year, it had transferred 50 equipment units from the Dresden factory to Amkor in Porto, and the first customer products have passed the certification required for GlobalFoundries equipment. Currently, GlobalFoundries is transferring some of its 300mm production lines from the Dresden factory to Amkor's Porto factory (which has passed the IATF16949 certification) to establish the first large-scale packaging and testing factory in Europe.
Powertech Technology
Although Powertech Technology, an established packaging and testing manufacturer, did not build a new packaging and testing factory in the past year, it also intends to expand overseas to achieve supply chain diversification.
In January of this year, Powertech's chairman, Tsai Du-Kung, said, "The company is evaluating the proposal to establish a high-end chip packaging factory in Japan, but this plan will only be advanced if we can find partners to invest together."
Tsai Du-Kung said that operating a chip assembly and packaging factory in Japan is more expensive than in Taiwan, so it only makes sense to do advanced or high-end chip packaging technology there. Currently, Powertech is negotiating with customers to assess their interest in investing in Japan.
He pointed out that the cost of operating a chip packaging factory in Japan is about twice that in Taiwan. However, he cited TSMC's Kumamoto project as an example of the advantages of a joint venture. "We believe that TSMC's business model in Japan is quite successful, and the company is exploring to follow this model, which may make operations there more sustainable. If the plan in Japan does not materialize, the company may consider expanding to Southeast Asia in the future."Long Electric
Domestic packaging and testing manufacturer, Long Electric Technology, has also made new moves in the past year.
On June 21, 2023, the new plant for Long Electric's wafer-level microsystem integration high-end manufacturing project in Jiangyin, Wuxi, was capped. The project, which started in July 2022, focuses on the world-leading 2.5D/3D high-density wafer-level packaging and other high-performance packaging technologies. It aims to meet the rapidly growing market demand from global customers for high-performance, high-computational power chips, providing a one-stop service from packaging co-design to chip finished product manufacturing. The first phase of the project is scheduled to be completed and put into use at the beginning of 2024, and the overall construction is progressing rapidly as planned.
In June 2023, Long Electric Technology signed the "Shanghai State-owned Construction Land Use Right Transfer Contract" with the Management Committee of the Lin-gang Special Area of the China (Shanghai) Pilot Free Trade Zone. It plans to establish the Long Electric automotive chip finished product manufacturing and packaging project in the Lin-gang Park of the Minhang Development Zone, covering an area of about 214 acres.
The project covers an area of 210 acres, with a construction area of about 200,000 square meters. The initial plan is for a 50,000 square meter clean factory, which is expected to be completed at the beginning of 2025. The project products cover the intelligent cockpit, intelligent interconnection, safety sensors, and module packaging types in the field of semiconductor new four-in-one, fully covering traditional packaging and future-oriented module packaging and system-level packaging products.
Long Electric stated that, relying on the group's complete packaging technology system, the Lin-gang project of Long Electric Technology will become the largest and most comprehensive automotive electronic chip manufacturing benchmark factory in China.
Tongfu Microelectronics, a domestic company, has taken steps to expand abroad in recent years.
In September 2023, Tongfu Microelectronics stated that the construction of the new plant of Tongfu Super Micro Penang in Malaysia is progressing smoothly and is expected to be completed and put into use within 2023.
Tongfu Super Micro is a joint venture between Tongfu Microelectronics and AMD. As early as 2016, Tongfu Microelectronics acquired 85% of the equity of AMD's production base in Penang, Malaysia, and had a packaging and testing platform in Malaysia, undertaking high-end product packaging and testing business for domestic and foreign customers.
In June 2023, the construction ceremony of the new plant of Tongfu Super Micro Penang was launched, with a total planned investment of nearly 2 billion ringgit (about 430 million US dollars). The new plant will further increase the supply capacity to AMD. According to the semi-annual report of Tongfu Microelectronics, the company not only provides packaging and testing services for overseas customers such as AMD but has also mass-produced Chiplet products for AMD.Huatian Technology
Huatian Technology is also building a new packaging and testing factory.
In March 2023, Huatian Technology announced that its wholly-owned subsidiary, Huatian Technology (Jiangsu) Co., Ltd., invested 2.858 billion yuan in the construction of the "High Density and High Reliability Advanced Packaging and Testing Research and Industrialization" project.
The announcement shows that the High Density and High Reliability Advanced Packaging and Testing Research and Industrialization project will build a new plant and supporting facilities of about 170,000 square meters, and purchase 476 sets of main production process equipment and instruments. After the project is completed and put into operation, it will form an annual packaging and testing capacity of 840,000 wafer-level integrated circuits for Bumping, 480,000 for WLCSP, and 26,000 for ultra-high density fan-out UHDFO. The construction period of the project is 5 years, from June 2023 to June 2028, and the project is carried out in a way of building and producing at the same time.
Huatian said that the project is mainly positioned in the high market demand and good application prospects of bump packaging, wafer-level packaging, and ultra-high density fan-out packaging. The main products of the project are Bumping, WLCSP, UHDFO, etc., and are applied to strategic emerging fields such as 5G, the Internet of Things, smart phones, tablet computers, wearable devices, medical electronics, security monitoring, and automotive electronics.
In conclusion,
With the slowdown of Moore's Law, more manufacturers have begun to pay attention to integration and packaging. In addition to traditional outsourcing packaging and testing manufacturers (OSAT), traditional IDM foundries have also participated in the packaging market. Whether it is traditional packaging or advanced packaging, the competition will only become more intense in the foreseeable future.
In the past year, while a large number of packaging and testing factories have been put into place, more new packaging and testing projects have been launched. At the beginning of 2024, a new round of packaging factory construction competition has already started. With the emergence of more advanced packaging technologies, who will be the biggest winner? Let's wait and see.
Post a comment