Introduction: The Rayleigh criterion has always been the fundamental principle followed in the development of lithography machines and is revered as the "golden rule" by the lithography industry. At the same time, there are tens of thousands of theoretical and experimental academic papers published on "breaking through the Rayleigh criterion," which have made many "highly cited scientists in the world." So, will the end of the Rayleigh criterion, BEUV (Beyond Extreme Ultraviolet) lithography machines, evolve into the grand finale of lithography machines? What challenges does the commercialization process of BEUV lithography machines face?
Preface
Chips are known as the "industrial food" of modern society and are the cornerstone of the information industry. Since the birth of integrated circuits in 1958, the chip industry has increasingly become a strategic, basic, and leading industry in national economic and social development. Chips have profoundly changed the way humans produce and live. From C-end products oriented towards mass consumers such as mobile phones, home appliances, and automobiles, to B-end products oriented towards business such as medical equipment, power, transportation, telecommunications, and electronic government affairs, and then to equipment in the national defense field such as satellites, missiles, and aircraft carriers, all cannot do without small chips. The so-called "three hundred and sixty lines, line by line with chips."
Advertisement
The process of a chip's birth is extremely long, going through many tests, which can be divided into three stages: chip design, front-end process (chip manufacturing), and back-end process (sealing and testing). The front-end process is the core link of the chip industry chain, which refers to the manufacturing process of chips based on the chip design layout, using the method of Lego building, with the wafer as the foundation, and carrying out processes such as diffusion, thin film, lithography, etching, ion implantation, chemical mechanical polishing (CMP), metallization, and measurement on the chip or medium substrate, layer by layer, and finally transferring the circuit diagram designed by the chip design company to the wafer and achieving the predetermined chip electrical function.
The nine major equipment of the front-end process mainly includes: diffusion furnace, thin film deposition equipment (including PECVD, LPCVD, ALD, etc.), lithography machine, photoresist coating and development machine, etching machine, ion implantation equipment, CMP, measurement equipment, and cleaning equipment.
In the chip manufacturing process, the level of lithography technology directly determines the minimum linewidth of the chip, defines the feature size of the semiconductor device, and directly determines the process level and performance level of the chip. There is no doubt that the lithography process is the most technically challenging, most costly, and longest cycle link in the chip manufacturing process. Advanced technology node chip manufacturing requires 60-90 lithography processes, with the lithography cost accounting for about 30% and the time consumption accounting for about 40-50%.
The lithography machine is the leader of the nine major equipment in the front-end process, accounting for about 20% of the total investment in the chip production line. The lithography machine integrates the latest scientific achievements of more than 40 disciplines such as physics, ultra-precision optics, precision instruments, polymer physics and chemistry, mathematics, materials, automatic control, fluid mechanics, high-precision environmental control, and software. In the development process of more than 60 years, the lithography machine (including its parts) has continuously challenged the limits of human ultra-precision manufacturing equipment and is known as the "flower of modern optical industry" and the "pearl on the crown" of the chip industry.
The Rayleigh criterion has always been the fundamental principle followed in the development of lithography machines and is revered as the "golden rule" by the lithography industry. The current development of lithography machines has entered the high-NA (Numerical Aperture) EUV lithography era, with a process that can reach 2nm and below, and is expected to start mass production in 2025.
So, how will the post-NA EUV lithography machine evolve? Will the BEUV (Beyond Extreme Ultraviolet) lithography machine evolve into the grand finale of lithography machines?The Birth of the Rayleigh Criterion
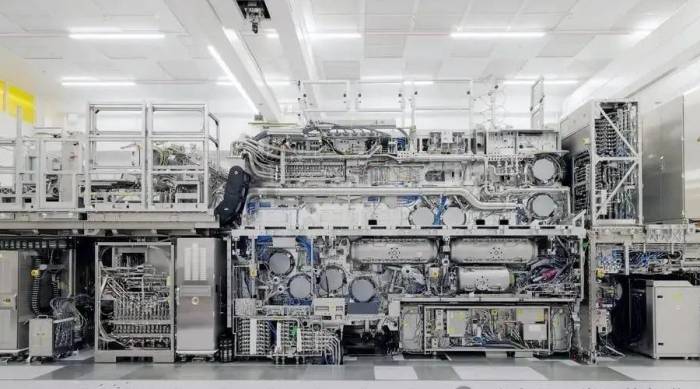
To address these questions, it is imperative to first look back at the history of the Rayleigh criterion.
This inevitably brings to mind three outstanding scientists: the British Royal Astronomer George Biddell Airy (1801-1892), the German physicist Ernst Abbe (1840-1905), and the British physicist Lord Rayleigh (1842-1919).
In 1835, George Biddell Airy provided a theoretical explanation of circular aperture diffraction in a paper titled "On the Diffraction of an Object-glass with Circular Aperture," and for the first time, he explicitly presented the concept of the diffraction limit.
Based on the diffraction properties of light, an infinitely small ideal light point, after being imaged through any size of a "perfect" lens (in reality, each lens has a limited aperture and has aberrations), will also form a diffuse pattern, that is, a circular spot with alternating light and dark. The central bright spot bounded by the first dark ring is called the "Airy disk." In short, the center of the Airy disk is a bright area, surrounded by a series of concentric rings with continuously decreasing brightness.
In 1863, Ernst Karl Abbe became a lecturer (Privatdozent) at the University of Jena. In 1866, Carl Zeiss (1816-1888) hired the then 26-year-old Abbe as an independent researcher to engage in the design and research of optical microscopes. It should be noted that Abbe's physics lectures also required optical instruments manufactured by the Zeiss company. In 1872, Abbe resigned from his position at the University of Jena and officially joined the Zeiss company.
In 1873, based on the principle of the "Airy disk," Abbe proposed the "Abbe optical diffraction limit theory" (Diffraction limitation), defining the resolution as follows:
\[ \text{Resolution} = \frac{\lambda}{2(n\sin\alpha)} \]
Here, \( \lambda \) is the wavelength of light, \( n \) is the refractive index of the medium between the sample and the microscope objective, and \( \alpha \) is the aperture angle of the microscope objective.Abbe was the first scientist to define the term numerical aperture. Specifically, NA = nsinθ, represents the numerical aperture of a lens imaging system. Consequently, the resolution can also be defined as:
In short, the smallest detail that a traditional optical microscope can detect is half the wavelength of light. This classic formula is inscribed on Abbe's tombstone.
In 1884, Abbe and Otto Schott (Friedrich Otto Schott, 1851-1935) founded the Schott Glass Works in Jena.
As is well known, currently, the lens system of EUV lithography machines is manufactured by Zeiss, and the ultra-low thermal expansion glass used in the lens system comes from Schott.
In 1896, the British physicist Rayleigh, based on the "Airy spot" theory, further extended and refined the "Abbe optical diffraction limit theory," establishing the "Rayleigh criterion." If the central brightest part of the diffraction pattern of a point light source just coincides with the first darkest part of the diffraction pattern of another point light source, Rayleigh believed that these two point light sources can just be resolved by this optical instrument.
The "Rayleigh criterion" is the first criterion that clearly gives the resolving power of an optical instrument. Under this criterion, the resolution of the optical instrument is:The Rayleigh criterion is commonly used in the field of optical imaging, including microscopes, telescopes, photography, and other optical imaging devices, and is used for the calculation of the highest spatial resolution of various optical instruments currently available. The Rayleigh criterion provides us with a standard for determining whether the details of an object can be resolved by an optical microscope, and also guides us on how to improve the resolution of the microscope, for example, by choosing a shorter radiation wavelength, increasing the refractive index, or using a microscope with a larger half-aperture angle, among other methods.
Rayleigh's research work covered multiple fields such as electricity, acoustics, and optics. In 1904, the Nobel Prize in Physics was awarded to Rayleigh in recognition of his research on the densities of some of the most important gases and for the discovery of argon during these studies.
The Rayleigh criterion formula for lithography machines is as follows:
\[ \text{CD} = \frac{k_1 \cdot \lambda}{NA} \]
Where CD is the critical dimension of the lithographic pattern, the minimum linewidth that the optical system can achieve on the wafer, i.e., the resolution of the lithography machine, \( k_1 \) is a process factor, and DoF is the lithographic depth of focus, \( k_2 \) is a process factor.
Thus, the Rayleigh criterion is an expression of wavelength and numerical aperture, which describes the resolution limit in the diffraction-limited system of a lithography machine, and has become the fundamental principle followed in the development of lithography machines. For nearly 60 years, it has been revered as the "golden rule" by the lithography industry.
Evolution of Optical Lithography Machines under the Rayleigh Criterion
The Rayleigh criterion indicates that two points on an object will be resolved when the distance between them is greater than a specific value. This specific value is related to the wavelength of the incident light and the numerical aperture NA. In the lithography process, the limit of resolution directly determines the smallest feature size that the lithography machine can manufacture. Designers and engineers of lithography machines must optimize the design and manufacturing of lithography machines based on the Rayleigh criterion to improve the lithographic resolution limit, allowing the distance between two distinguishable points by the lithography machine to become increasingly smaller. According to the Rayleigh criterion, there are mainly three ways to improve the resolution of a single lithography exposure:
1. Shorten the exposure wavelength;
2. Increase the numerical aperture NA of the projection lithography lens;
3. (The third method is not provided in the original text, so it is not translated here.)3. Reduce lithography process factors.
In addition to resolution, depth of focus (DoF) is also a key parameter. In the actual lithography process, the lithography machine's lens has a focal point, and around this focal point, there is a range within which the wafer surface can move vertically. As long as the thickness of the photoresist (i.e., the photosensitive layer) is within this range, the entire layer can be clearly exposed without causing a significant decrease in lithography resolution.
Generally speaking, the higher the lithography resolution, the smaller the depth of focus. That is to say, the process tolerance allowed by lithography is smaller. In actual operation, the surface position of the wafer has nanometer-scale variations, which can also cause the details of the pattern to become blurred and have a significant impact on the lithography results. This puts forward more stringent requirements for the leveling and focusing system of the lithography machine.
The first way to improve lithography resolution is that the wavelength of the lithography machine has gone through a development process from 435nm (G-line), 365nm (I-line), 248nm (deep ultraviolet, DUV), 193nm (ArF, dry and immersion) to the current 13.5nm (extreme ultraviolet, EUV).
The second way to improve lithography resolution is that the larger the numerical aperture (NA), the more diffraction beams are collected, and the higher the lithography resolution. The numerical aperture (NA) of the DUV lithography machine's projection lens has also increased from 0.4 to 0.93. In the 193nm immersion lithography machine, due to the water filled between the wafer and the lens, the numerical aperture (NA) can reach up to 1.35. For EUV lithography machines, the numerical aperture (NA) has increased from 0.33 to 0.55.
The third way to improve lithography resolution is that the resolution of the lithography system can also be improved by optimizing process parameters. For example, off-axis illumination, computational lithography, and photoresist process, etc., are used to reduce the process factor k1. The single exposure k1 reflects the actual situation in the lithography process, and its theoretical limit is 0.25.
To further reduce the process factor k1, multiple exposure technology has also been proposed. In theory, "193nm immersion technology" + "multiple exposure" can be applied to the production of chips at the 3nm node. However, in practice, when the chip enters the 7nm node, the process complexity rises sharply, and its process steps are five times that of EUV lithography, and the lithography times are three times that of EUV lithography, resulting in the difficult-to-solve "80% chip yield" problem. And an 80% chip yield is usually the standard for chip factories to achieve profitability.
Before 2023, the most advanced EUV lithography machines of ASML were TWINSCAN NEX:3400C and TWINSCAN NEX:3400D, with a price of about 170 million euros. Its NA is only 0.33, corresponding to a resolution of 13nm, which can produce chips with metal spacing between 38-33nm.In December 2023, the high-NA EUV lithography machine developed by ASML was delivered to Intel Corporation's D1X factory in Oregon, USA, for installation. The factory has become the base for Intel's most cutting-edge research and is also the place where the company develops each generation of chip technology.
On February 10, 2024, ASML showcased the high-NA EUV lithography machine to the media, with the model number TWINSCAN EXE:5000, and an NA of 0.55. The lithography resolution per exposure reached 8nm, with a price tag of 350 million euros (approximately 2.7 billion yuan). Intel Corporation has completed the development of the Intel 18A (1.8nm) and Intel 20A (2nm) manufacturing processes. The aforementioned chip processes may utilize the high-NA EUV lithography machine to some extent. In addition to Intel, TSMC, Samsung Electronics, SK Hynix, Micron, and other leading wafer manufacturers are actively competing to purchase or have the intention to purchase ASML's new generation of high-NA EUV lithography machines.
Undoubtedly, so far, the Rayleigh criterion remains the fundamental principle for the development of lithography machines.
Scientific and experimental breakthroughs of the Rayleigh criterion
The Rayleigh criterion is a cloud hanging over the heads of researchers in microscopic imaging and lithography technology. Entering the 21st century, various super-resolution imaging technologies have broken through the limitations of the diffraction limit and the Rayleigh criterion, bringing about a new revolution in microscopic imaging technology.
In the field of microscopic imaging, the typical super-diffraction limit imaging technologies are mainly divided into three categories: structured illumination microscopy (SIM), stimulated emission depletion microscopy (STED), and single molecule localization microscopy (SMLM). The most famous is the STED imaging technology. In 1994, Professor Stefan W. Hell of the Max Planck Institute for Biochemistry in Germany published the STED theory in the "Optics Letters" magazine. For this outstanding work, Professor Stefan W. Hell was awarded the 2014 Nobel Prize in Chemistry.
The STED imaging technology originates from Einstein's stimulated radiation theory and is a super-resolution fluorescence imaging technology. The basic principle can be understood as: since the diffraction effect causes a diffraction spot, find an "eraser" to erase the edge of the diffraction spot, so that it can break through the Rayleigh criterion.The purpose of super-resolution imaging is to magnify tiny objects for human observation. However, the reverse photolithography process (projection reduction) is also feasible. Inspired by STED imaging technology, in 2009, photolithography researchers proposed a fast super-resolution direct writing photolithography technology based on monochromatic edge suppression. A 532 nm femtosecond laser is used as a "pencil light" to form a solid light spot, achieving two-photon absorption excitation polymerization of photoresist; another 532 nm continuous laser is used as an "eraser light" to form a hollow dark spot, achieving single-photon absorption suppression polymerization. These two light spots are nested together, which can achieve the effect of super-resolution lithography. It has already achieved a minimum linewidth of 36 nm and a minimum resolution of 140 nm for super-resolution writing.
Surface plasmon super-resolution lithography modulates the spectral distribution of the diffraction of the object shape of the surface plasmon lens, combined with the control of the electric field components on the image plane, to achieve the amplification enhancement of the evanescent wave, and transform the object image into a near-field evanescent wave form for lithography. In theory, surface plasmon super-resolution lithography is not limited by the Rayleigh criterion. Since the equivalent wavelength of surface plasmons can reach the X-ray level, it can achieve a lithography effect below 22 nm on the i-line, which is 0.24 times the traditional diffraction limit.
Nanoimprint lithography (NIL) equipment is also an important way to break through the Rayleigh criterion. Its principle is very simple, using the traditional mechanical mold micro-replication principle, similar to printing technology, applying photoresist on the wafer, and then pressing a mold with a specific pattern to directly form complex 2D or 3D patterns by pressing.
On October 13, 2023, Canon Inc. of Japan announced the launch of the nanoimprint equipment FPA-1200NZ2C that can manufacture cutting-edge chips. Canon Inc. of Japan claims that this equipment can achieve a minimum linewidth of 14 nm patterning, equivalent to the 5 nm node. With further improvements in mask technology, NIL is expected to achieve a 2 nm node. The equipment, because it does not use lenses, will have a photolithography process cost that is "an order of magnitude less than ASML's EUV," and the power consumption will also be reduced by 90%.
It is widely believed that NIL technology is regarded as an alternative solution to traditional lithography technology, which can achieve lower-cost chip mass production in the 3D NAND integrated circuit field.
The proposal of BEUV lithography technologyThe International Roadmap for Devices and Systems (IRDS) is jointly formulated by industry, government, and academia. The IRDS continues the working model of the International Technology Roadmap for Semiconductors (ITRS), releasing a new 15-year roadmap every other year and updating it annually. The IRDS serves as a guiding light for the development of the chip industry.
The IRDS outlines the development needs for lithography technology by 2037. Although the latest model of the EUV lithography machine, the Twinscan EXE:5000 by ASML, can barely meet the current demands, its reduction ratio in the scanning direction is 8:1, while the reduction ratio in the vertical direction remains at the original 4:1 due to the limited angle range of high reflectivity of the multi-layer reflector. This results in a maximum exposure field size of 26mm x 16.5mm on the wafer, compared to the original EUV lithography machine with an NA of 0.33, which had a maximum exposure field size of 26mm x 33mm. This has a significant impact on the manufacturing of large-area chips and the productivity of EUV lithography machines.
The IRDS also provides a development forecast for lithography machines by 2037. In the long term, there are two options: EUV lithography machines with a higher NA (for example, an increase to 0.70) and BEUV (Beyond Extreme Ultraviolet) lithography machines with a wavelength of 6.X nm. The latter is more likely, mainly because the 6.X nm BEUV lithography machine has a larger depth of focus (DoF) than the 13.5 nm EUV lithography machine at the same resolution, which brings greater process tolerance.
Challenges faced by BEUV lithography machine technology
In the long term, the development of BEUV lithography machines can fully inherit the research results of the previous EUV lithography machines. However, it also faces some new technical challenges, mainly including 6.X nm light sources, 6.X nm multi-layer films, and 6.X nm photoresists.
Currently, there are several methods for generating EUV light sources, including laser-produced plasma (LPP), various accelerator light sources based on relativistic electron beams (including synchrotron radiation sources, free-electron lasers, and steady-state microbunches), discharge plasma (DPP) and laser-assisted discharge plasma (LDP), and high-harmonic EUV light sources.
The commercially available EUV lithography machines currently use laser-produced plasma EUV light sources. The principle is to generate 13.5 nm EUV light by the interaction of high-intensity lasers with target materials, causing the target materials to absorb high energy, vaporize, and produce high-temperature plasma. ASML's commercial EUV lithography machine light source uses a dual-pulse excitation scheme, which shapes and ionizes tin droplets. First, a picosecond pre-pulse laser with a wavelength of 1 micrometer accurately bombards a rapidly passing tin droplet with a diameter of about 27 micrometers, causing the droplet to expand and diffuse into a high-density dome-shaped distribution. Then, the main pulse of a CO2 laser with a diameter of several hundred micrometers and a repetition frequency of 50kHz accurately bombards the expanded tin droplet again, generating EUV light through the CO2 laser's excitation of plasma physics.Dual-Pulse Excitation Scheme for EUV Lithography Light Source
To achieve a high-brightness 6.X nm wavelength light source, currently, a Yb:YAG pulsed laser device with a wavelength of 1030 nm is used to irradiate a gadolinium (Gd) target material to generate plasma. Research results indicate that the EUV conversion efficiency of the Gd plasma is only 0.47%.
The EUV conversion efficiency of the actual EUV lithography machines in use today is about 5%. In short, the EUV conversion efficiency of the BEUV lithography machine is nearly an order of magnitude lower than that of the EUV lithography machine! Currently, a single EUV lithography machine consumes 30,000 kWh of electricity per day, while a BEUV lithography machine could reach 300,000 kWh!
Of course, the 6.X nm light source based on laser plasma of target materials such as gadolinium (Gd), terbium (Tb), aluminum (Al), magnesium (Mg), and magnesium-copper-gadolinium alloy (Mg65-Cu25-Gd10) is still under development, and there should be room for improvement in the BEUV conversion efficiency.
The design of the 6.X nm multilayer film is similar to the traditional EUV multilayer film design, both originating from thin-film interference theory. However, the reflectivity of the commercialized 13.5 nm Mo/Si multilayer film has reached a maximum of 69.5%, with a lifetime of 30,000 hours. Theoretically, La/B is an excellent structure for the 6.X nm multilayer film, with a theoretical reflectivity of over 78%! However, the actual research results of the 6.X nm multilayer film reflectivity are quite disappointing, less than 60%! This will greatly increase the heat of the mask and reflector in the projection optics, accelerating the aging and performance degradation of the 6.X nm multilayer film reflector.
A key issue faced by EUV photoresist is the stochastic effect. The absorption of EUV photons and secondary electron scattering by EUV photoresist are essentially random events. Stochastic effects can lead to defects, including uneven feature sizes and rough edges, and even serious defects such as missing contacts and bridging. The stochastic effect faced by BEUV photoresist is even more severe, mainly because the noise level of photon absorption will significantly increase at shorter wavelengths.
Several opinions on BEUV lithography machine technology
The following are the author's several opinions on BEUV lithography machine technology, and it needs to be particularly pointed out that these views represent the author himself.1. The research achievements of Airy, Abbe, and Rayleigh led to the emergence of the Rayleigh criterion. The Rayleigh criterion is widely applied in optical equipment such as microscopes, telescopes, photography, and lithography machines, providing a standard for people to judge whether the details of an object can be resolved by optical equipment.
2. Entering the 21st century, there are tens of thousands of theoretical and experimental academic papers on "breaking through the Rayleigh criterion" that have been published, making many "highly cited scientists worldwide." Various super-resolution imaging technologies have broken through the limitations of the diffraction limit, breaking through the Rayleigh criterion, and bringing a new revolution in micro imaging technology.
3. However, these "beyond the Rayleigh criterion" micro imaging technologies have not yet achieved large-scale commercialization. Conventional microscopes that follow the Rayleigh criterion (with a resolution of about 200nm) are still widely used in many fields such as scientific research, industrial production, medical treatment, and education, with a market size approaching 10 billion US dollars, and the market size continues to expand rapidly.
4. For nearly 60 years, the Rayleigh criterion has been the fundamental principle of lithography machine development and has always been regarded as the "golden rule" by the lithography industry. The wavelength of lithography machines has gone through five generations from 435nm to the current 13.5nm, and the numerical aperture NA of EUV lithography machines has also increased from 0.33 to 0.55, with the ultimate resolution reaching 8nm.
5. However, the development of high-NA EUV lithography machines still faces many challenges. In addition to the high price of 350 million euros, there are still many unacceptable shortcomings on the technical level, especially the maximum exposure field size is only 26mm × 16.5mm, which has a greater impact on the large-area chips and yield, making the lithography "area wall" problem more prominent.
6. The limitation of the Rayleigh criterion is a principle obstacle to the development of lithography technology and is a haze that hangs over the heads of lithography technology researchers. For this reason, various super-resolution lithography technologies are being studied, but the prospects for commercialization are still unclear. Nano-imprint technology has initially shown application prospects in the 3D NAND field, but the prospects for application in logic chips are not optimistic.
7. According to the Rayleigh criterion, the BEUV lithography machine with a wavelength of 6.X nm is one of the important choices to continue Moore's Law after 2037. Under the same resolution, the BEUV lithography machine has a larger depth of focus than the EUV lithography machine, bringing greater process tolerance.
8. The technology of the BEUV lithography machine is far from mature, including the 6.X nm light source with higher BEUV conversion efficiency, the 6.X nm multilayer film with higher reflectivity and longer life, and the 6.X nm photoresist to reduce random effects.
9. Although the technology of the BEUV lithography machine is far from mature, whether it can be commercialized depends more on the necessity of continuing Moore's Law than on technical breakthroughs. The reason is that the research progress of logic chips expanding performance through stacking methods is also continuously making progress.
10. The BEUV lithography machine fully inherits the research results of the previous EUV lithography machines. There is no doubt that as the only company that can produce EUV lithography machines, ASML holds a very advantageous position in the development of BEUV lithography machines.
Post a comment